Complete guide to DIY Retaining Walls
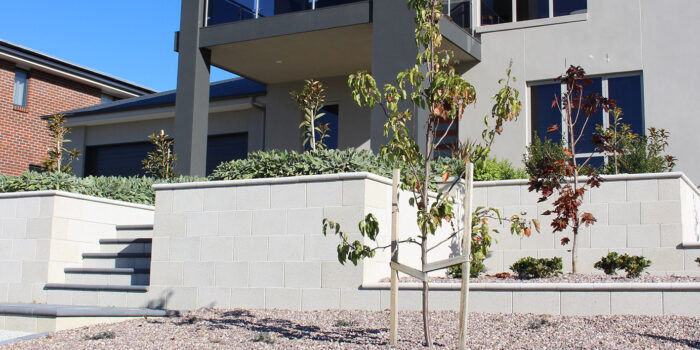
Before you get started on your DIY retaining wall, there are a few things you need to check before you begin.
At APC, we are here to help you every step of the way with our Complete Guide to DIY Retaining Walls. If you are still unsure on how to complete your project, visit us at APC and speak with our expert staff.
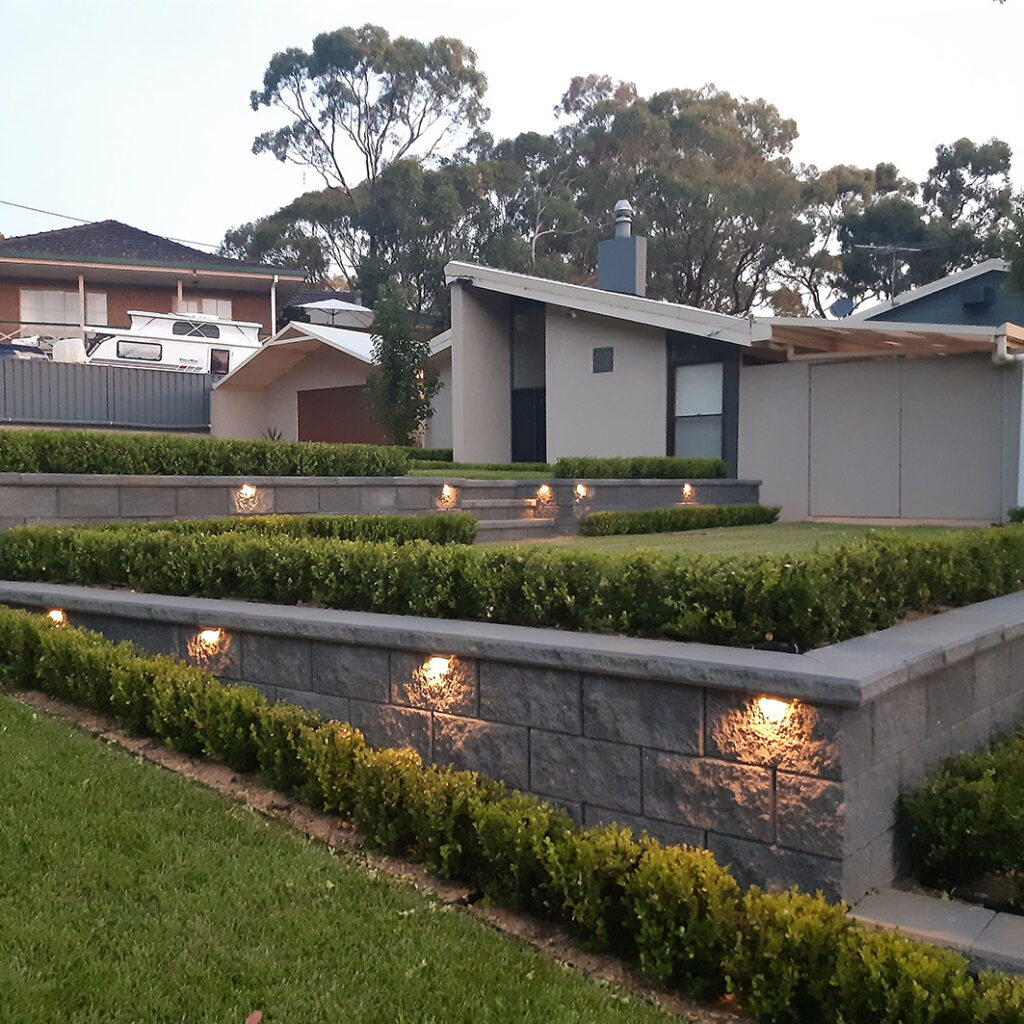
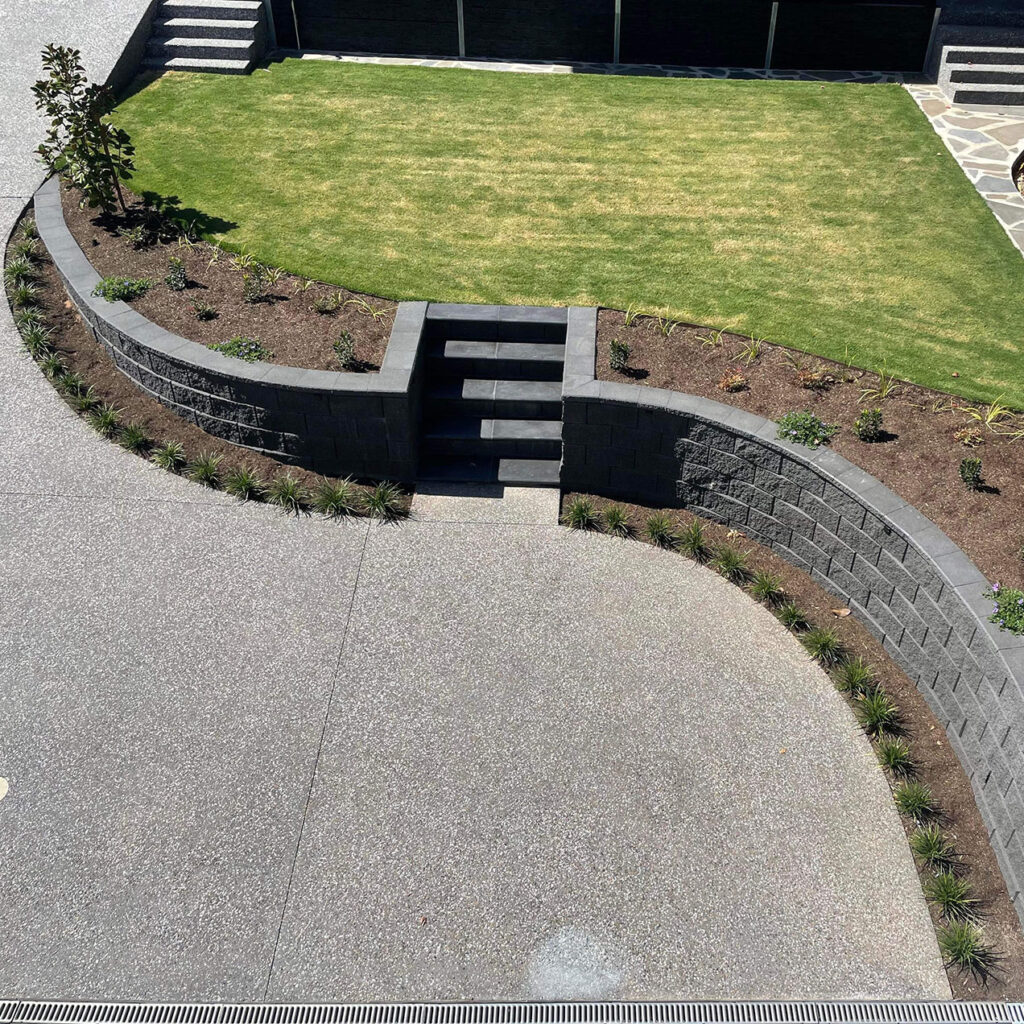
size and height of your wall
The most important question is the size and height of your wall as this will determine which products are best suited for the job. Some products can go higher than others without reinforcement and engineering.
When choosing your retaining wall blocks, be sure to read APC’s features, benefits and specifications on each type of block, to ensure they are suited to your particular project.
You should consider if you are building a curved or straight wall, do you need to incorporate steps, is it for an internal wall or on a boundary and do you want a terraced, vertical or step back wall.
Some retaining wall blocks are better suited for straight walls, some can be used for curved walls and some for near vertical high walls. All of them have a limit on the height they can be built to.
The team at APC will be able to advise you of which method would best suit your situation and budget.
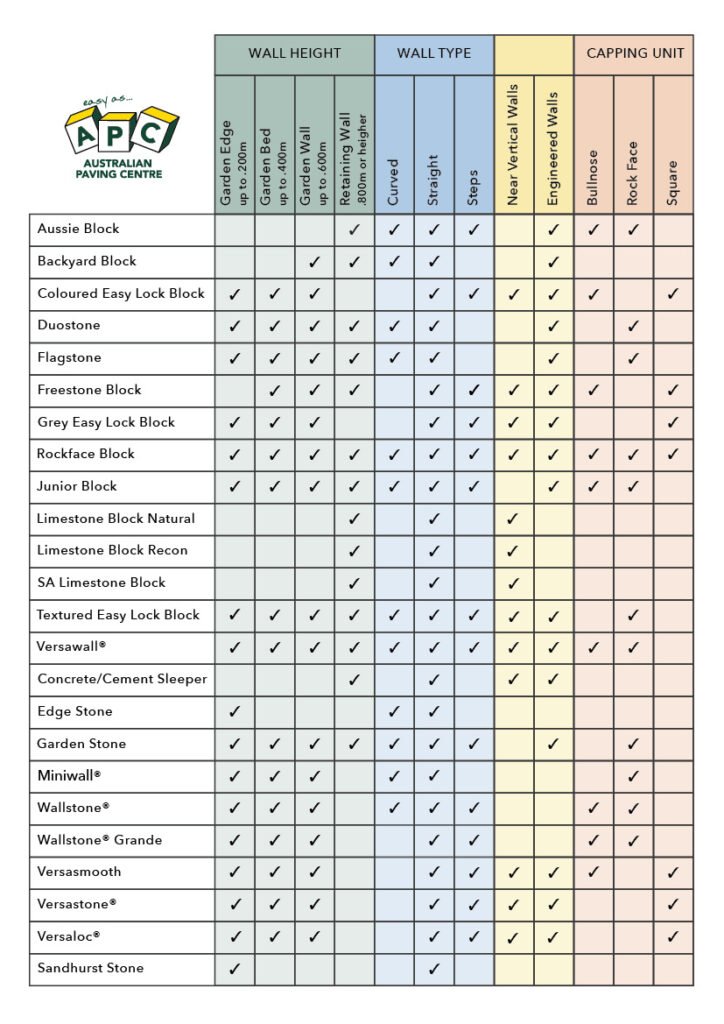
required tools and materials
- Ear muffs
- Eye protection
- Gloves
- Measuring tape
- Road base (allow up to 150mm deep)
- 10-20mm blue metal or screenings for block infill (if req) and backfill
- Spirit level
- 3mm metal straps or plates (for levels)
- Screeding bar
- Rubber mallet
- Wheelbarrow
- Spade / shovel
- String line (optional but recommended)
- Pegs or stakes
- Broom
- Marker spray paint
- Brush
- Compactor
- Brick saw
- Hammer and bolster (splitting blocks)
- Drainage pipe
- Sand
- Caulking gun
- Construction grade adhesive or tiling glue (for applying capping units)
- Walling product
Step 1 : Prepare the site
Correct preparation is the most important part of your project and if done correctly will save you time in the long run and ensure your wall will look great for years to come.
We recommend poisoning the grass/area two weeks prior to excavating as this will help you to prepare the area a little easier. Make sure you invest time in preparing a good foundation and be patient. It should be level and an even depth – if you start level, you should finish level! Correct preparation is key to ensure your wall is built correctly and evenly.
Excavation
Mark out the area on the ground where your wall is going to be with your marker spray paint. Dig out the marked areas to the required depth for your foundation plus half a block height, ensuring you remove any roots, debris and soft earth then compact the base of the trench.
Remember, before you undertake any job that requires excavation, you should check with ‘Dial before you Dig’ (www.1100.com.au) to avoid the risk or hitting storm water pipes, electrical lines or data cables.
The depth of your excavation should be 75mm to 250mm dependant upon ultimate height of block wall.
Once you have worked out the desired finished surface level :
- Drive stakes into the ground on the corners of the area to be prepare and run string lines between them at the finished surface level.
- Level the strings using a string line level.
- Mark out the area to be excavated with spray paint.
- Remove all grass from the area to be prepared.
- Excavate the ground to the required depth.
- Check evenness and depth of base by measuring from string line. The finished surface level of footing should be ½ a block depth below ground level.
Step 2 : Sub-grade
Correct base preparation is the most important part of every Retaining wall Project. The sub-grade is the natural soil that the foundation is supported on. This should be firm and all top soil and vegetation removed. Sub-grade should be trimmed to within 25mm of the desired level and compacted if necessary. Backfill for service trenches should be compacted in layers no greater than 150mm. Correct preparation of sub-grade reduces the incidence of shrinking and rutting. Trench should be clear of soft spots ponding water, trenches should be dewatered and cleaned prior to construction of foundation.
Step 3 : Screeding the road base foundation
Roadbase
Compacted Roadbase footing – this is most often used for standing gravity retaining walls where a roadbase is compacted and levelled. A sand leveling pad may be required to get precise level. All materials to be well compacted with a plate compactor.
Concrete Levelling pad footing – this is used when soil conditions are poor or when exceeding the maximum unreinforced wall heights and a concrete base is used with a construction grade adhesive applied to the first course of blocks.
Leveling pad
The leveling pad is to lay bedding sand evenly over the roadbase area to a maximum depth of 10-15mm. Bedding sand (washed concrete sand) is required to refine the finished level to lay the retaining wall blocks on.
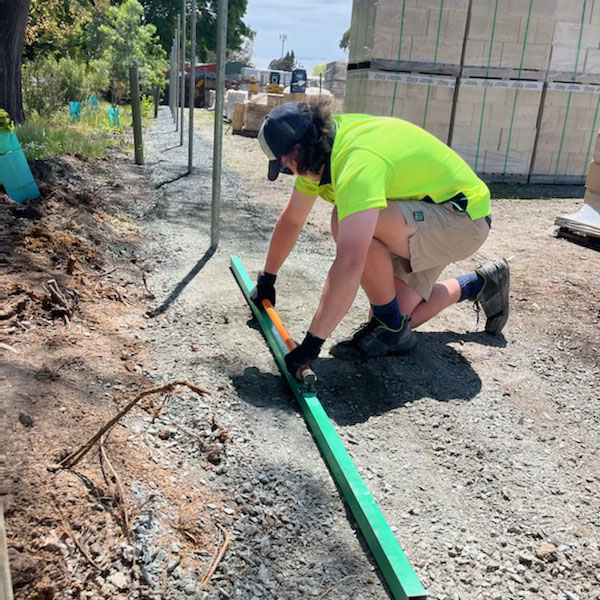
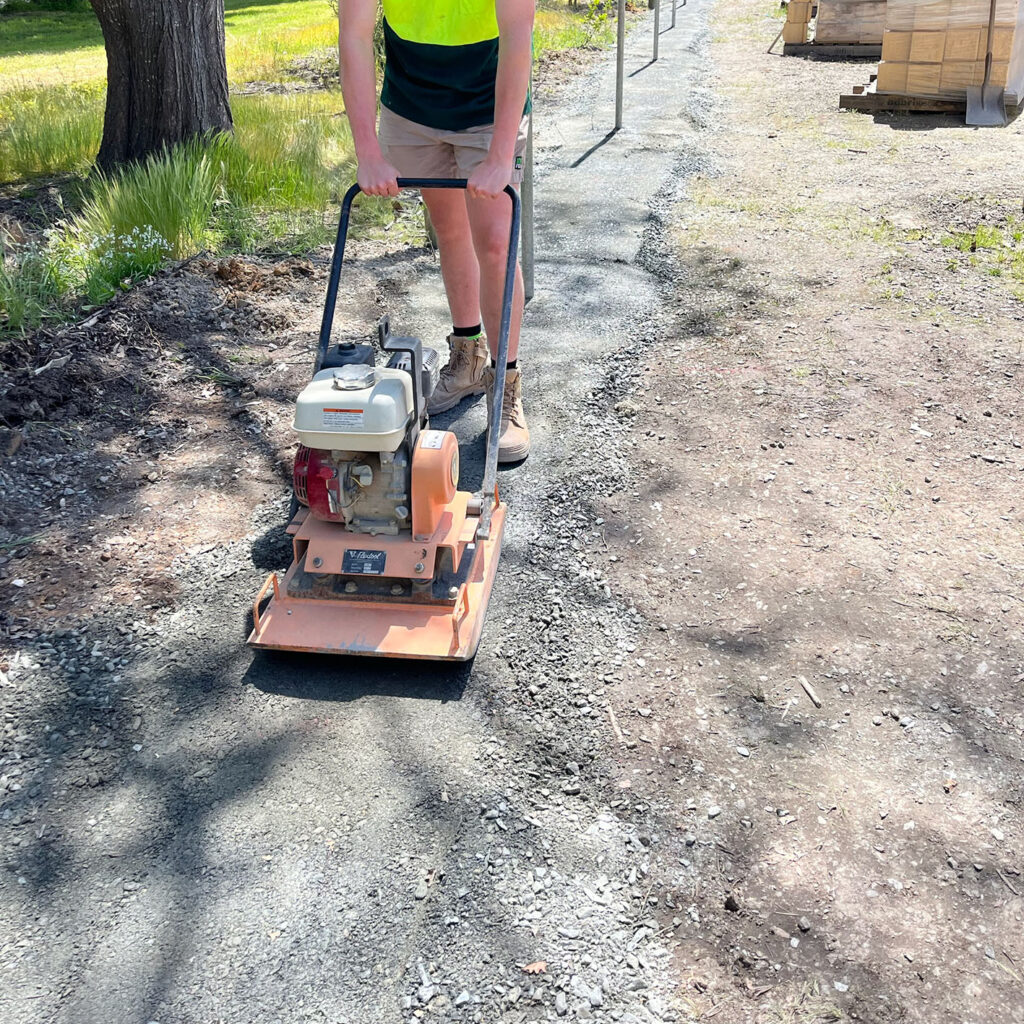
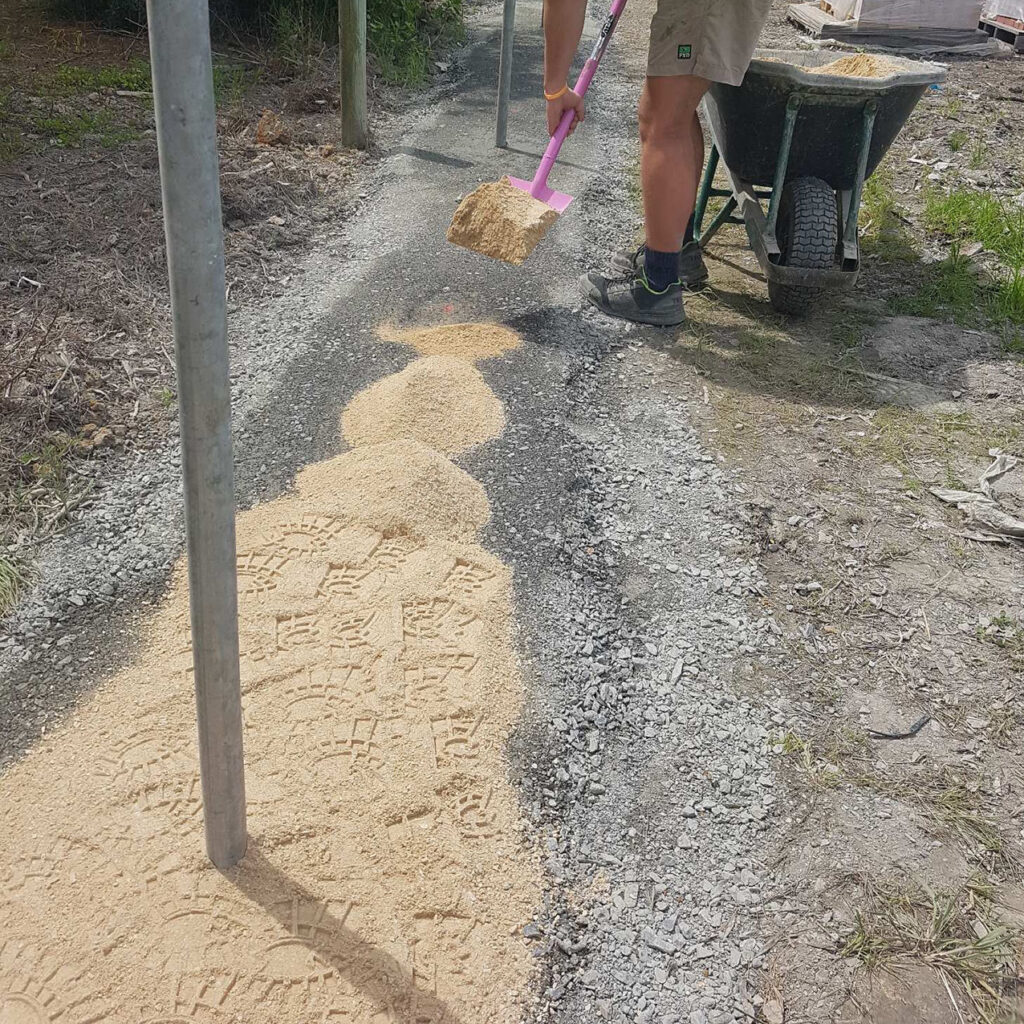
Step 4 : First course
The First course is now embedded into the leveling pad, the use of a level and string line is recommended to ensure first course is laid correctly. Ensure each block is filled with clean aggregate.
Drainage and back fill
Place 100mm pvc agricultural pipe (with sock if required) behind the wall, with a 1 in 100 fall. Backfill behind the courses of blocks to a width of 200-300mm using 10-20mm clean aggregate. Ensure each block is filled with clean aggregate.
Surface drainage
Surface drainage has to be taken into consideration, water cannot be allowed to cascade over the new wall, or flow on to areas where erosion or damage can be caused. If necessary create a swale drain on top of the wall to control water flow to the correct drainage point. Any agricultural pipe used should be vented to daylight.
Laying additional courses
Lay the next course and subsequent courses to a string line, following the same procedure, brush clean the top of the blocks, filling the cores and backfilling behind the blocks to a maximum one block high at a time.

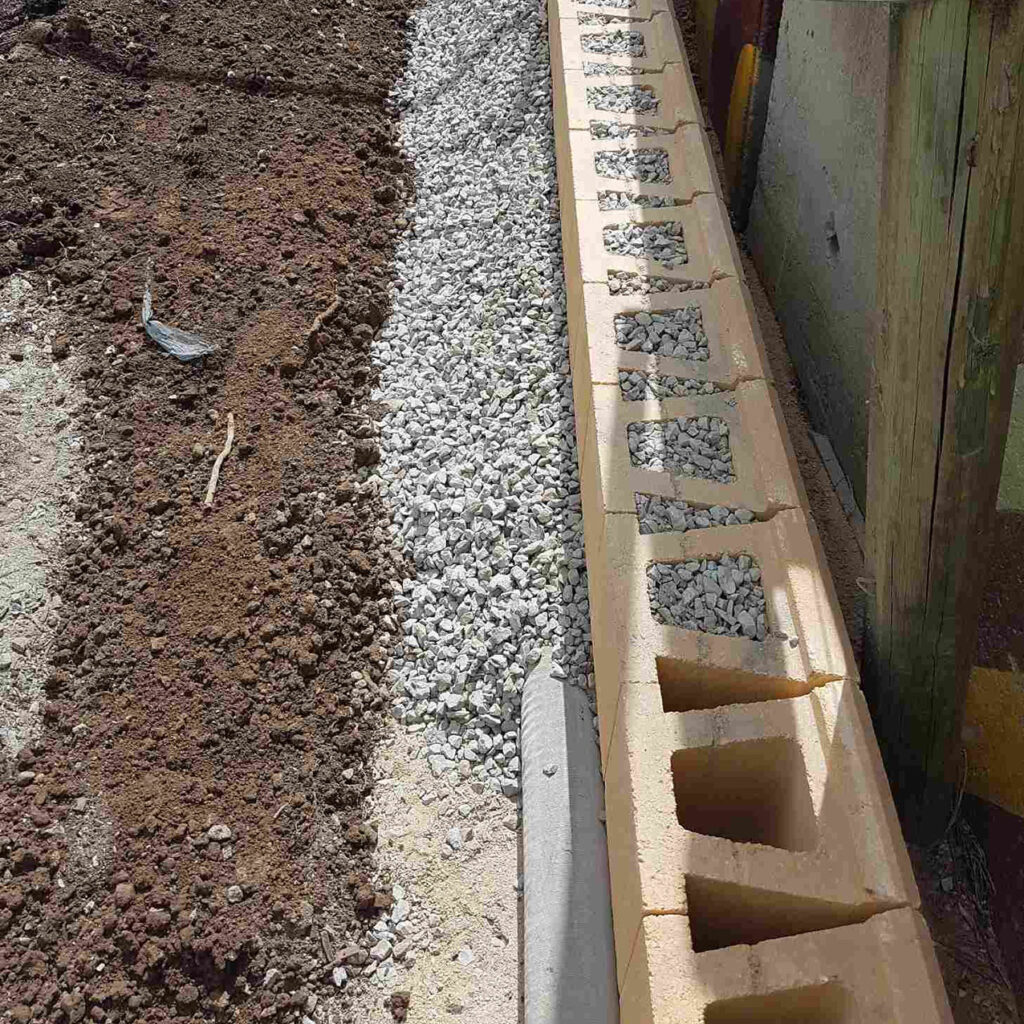
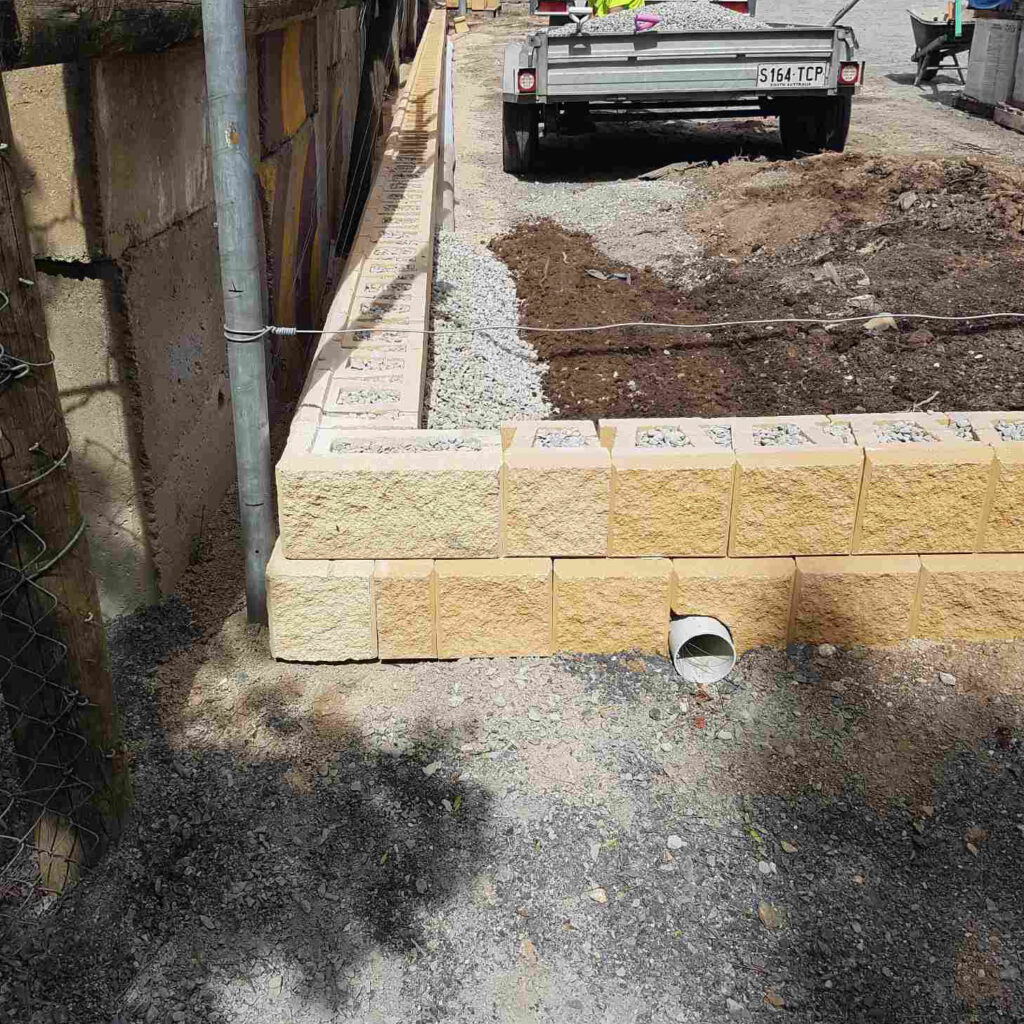
Step 5 : Cutting the caps
If your retaining wall has corners and you are required to cut caps, refer to our diagram on how to cut these to fit.
Fixing the caps
Caps are glued with a tiling cement for superior strength and durability.
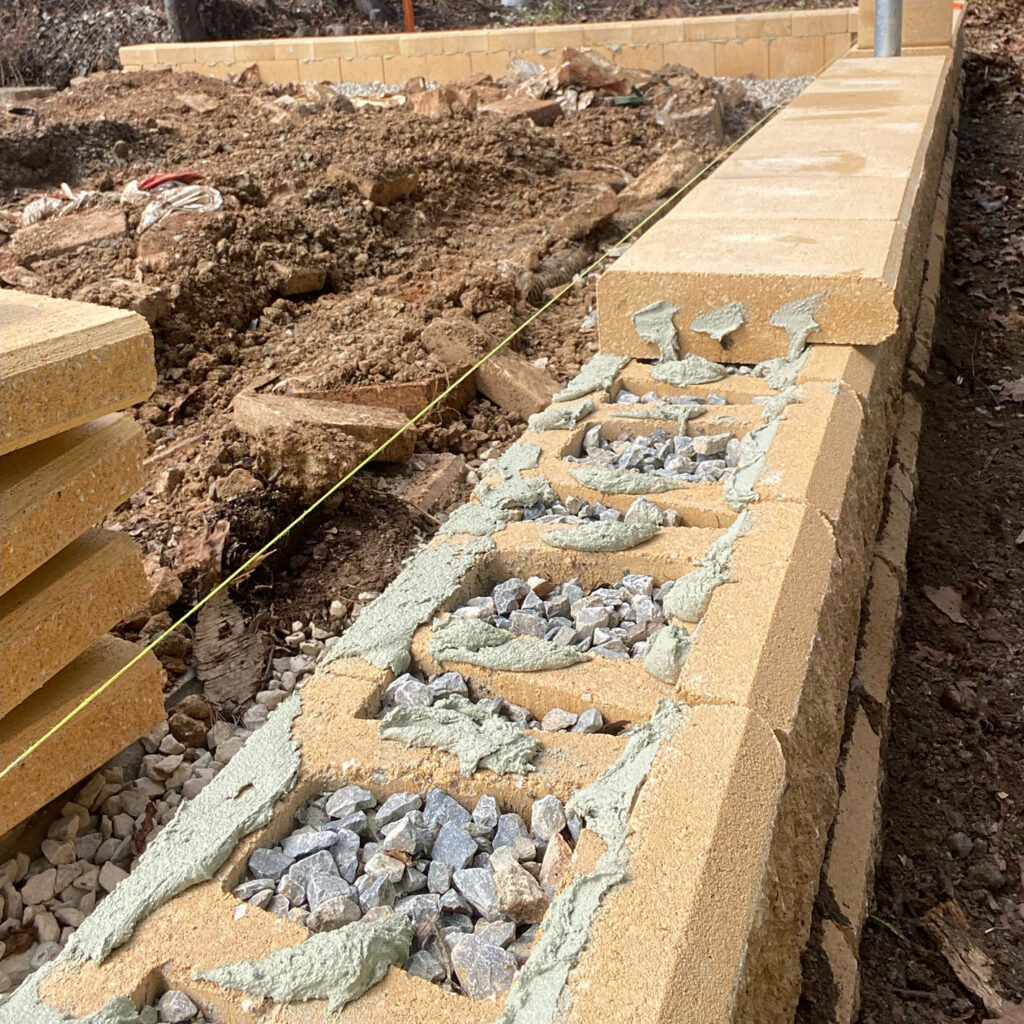
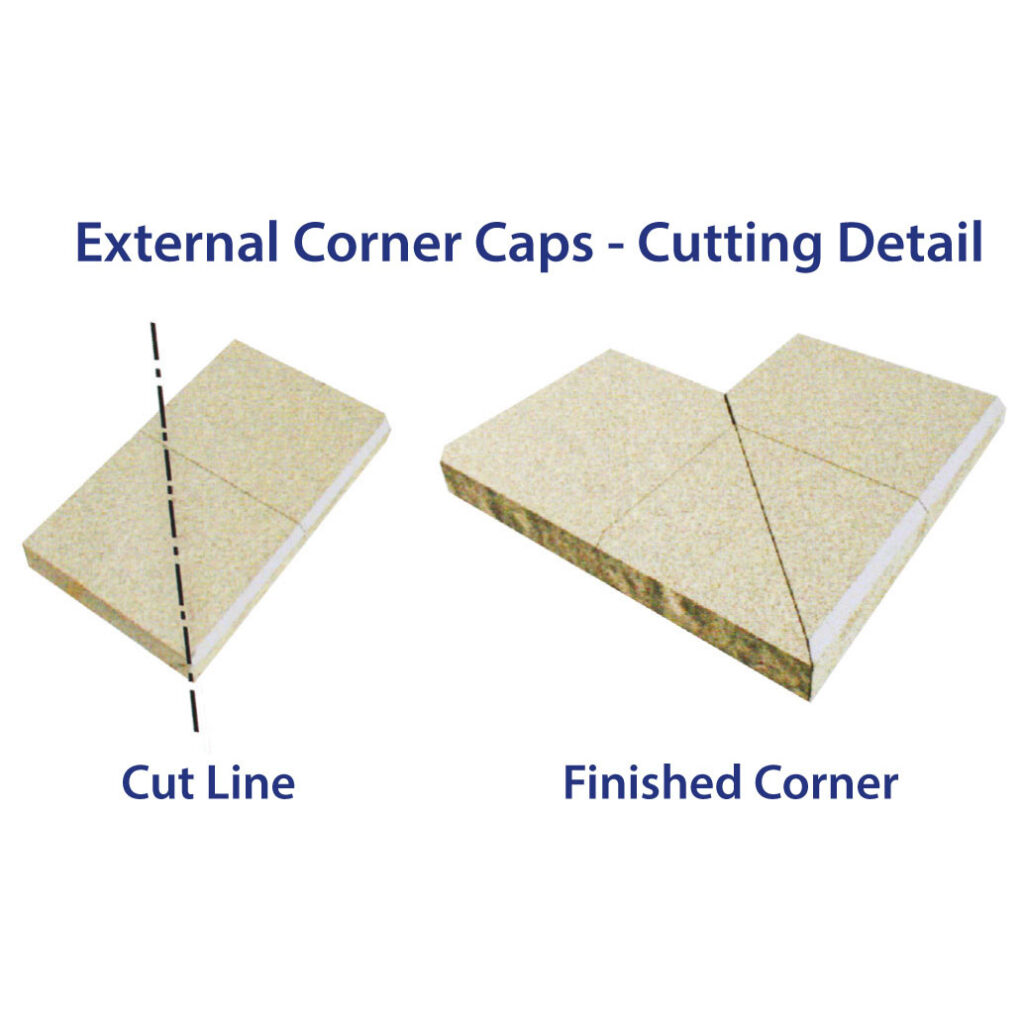
Wall Requirements
Corners
Working with vertical corners, start at the corner and work back ensuring corners are properly locked in, some construction adhesive may be necessary. Some product corners have a setback which makes corners more difficult to construct.
Some corner blocks are built by fixing the purpose made corner blocks alternately to each course using adhesive. Lugs must be removed from some of the blocks to ensure that the corner block fits evenly. Check with your local APC store on each system requirements.
A maximum height of 1 meter is recommended when using corner blocks. Curved corners are the preferred method of corner construction.
Curves
Curves and serpentine walls are easy to construct and the best guide is to lay out a garden hose and follow the profile. Mark the profile with spray paint. Be conscious that the length of courses will vary for a concave or convex wall. With fewer blocks per lineal meter of a convex and more blocks per lineal meter when the wall is concave. For convex curved walls knock the back wing off the block with a hammer. For concave walls simply position the blocks. Always keep the front of the blocks tightly together.
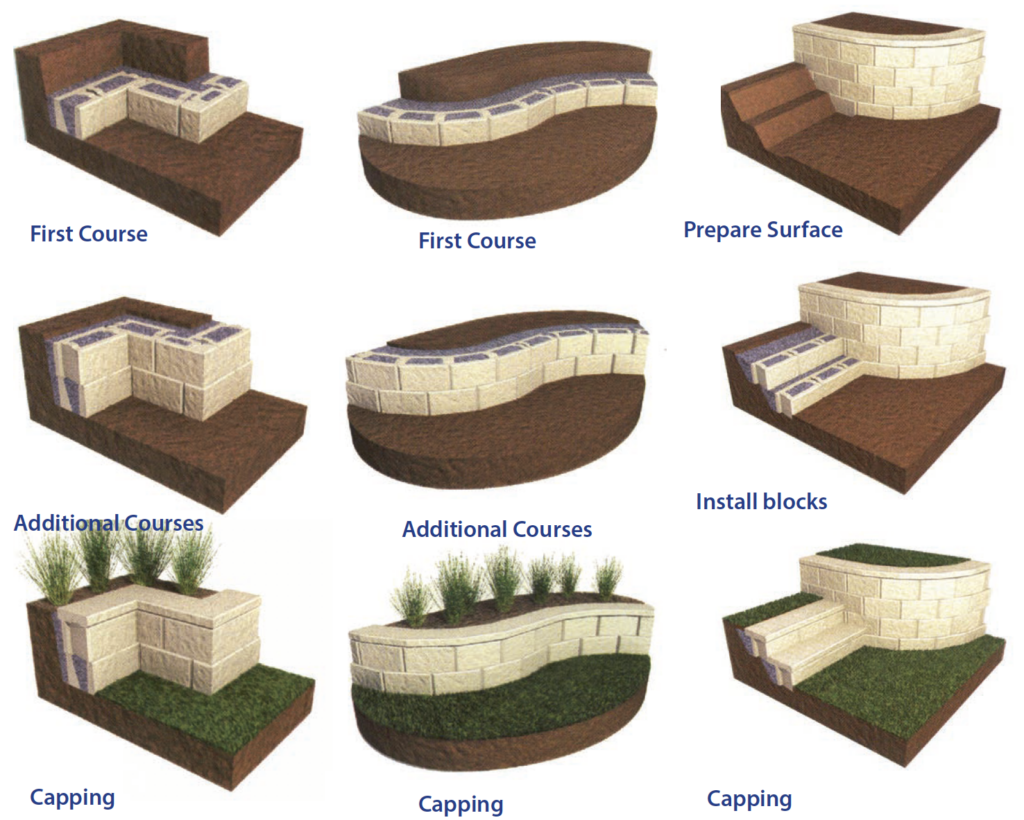
Wall Step Downs
Stepping down a wall can be easily achieved by using corners and half caps. All corners and caps must be fixed with tiling cement.
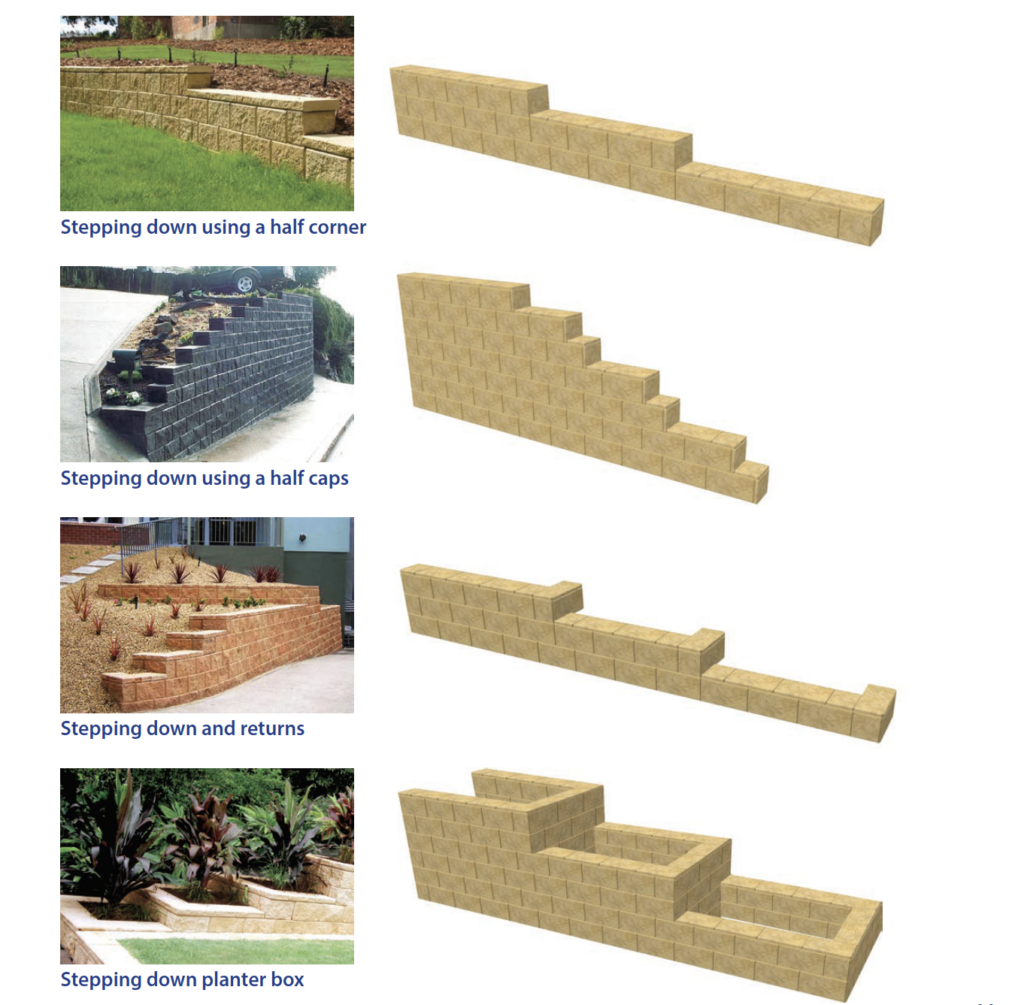
Understanding wall heights and types
The following diagrams are typical cross sections of various retaining wall applications. These designs are reflective of common applications but you should check with your local Council regarding requirements and regulations for retaining walls in your area and seek engineering advice if you have soil with high clay contents or for walls built over the maximum stated unreinforced heights.
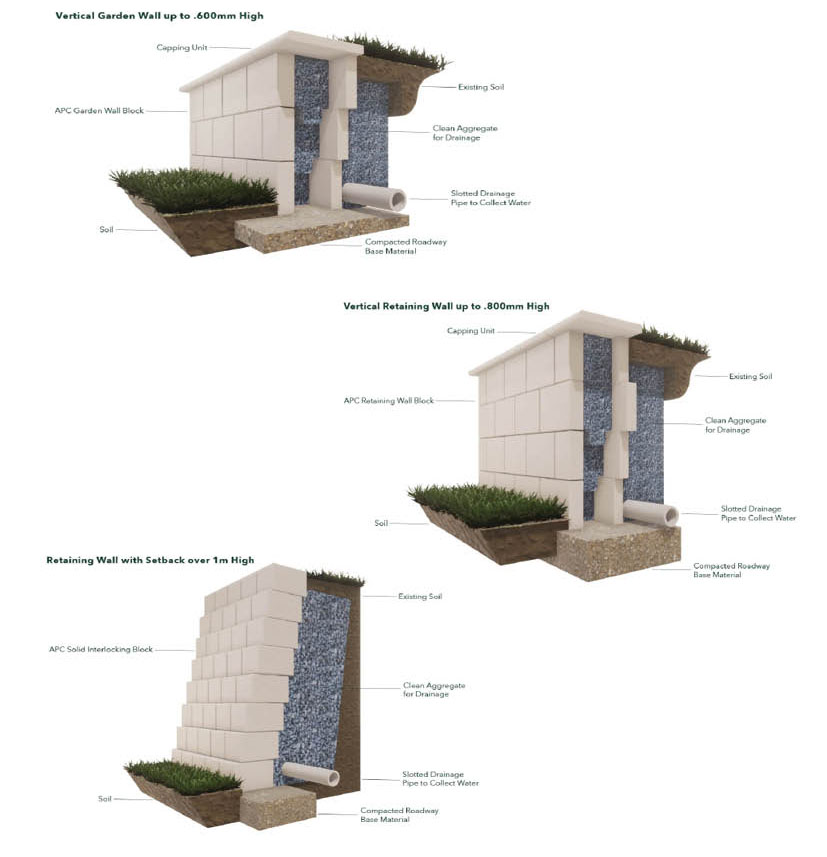
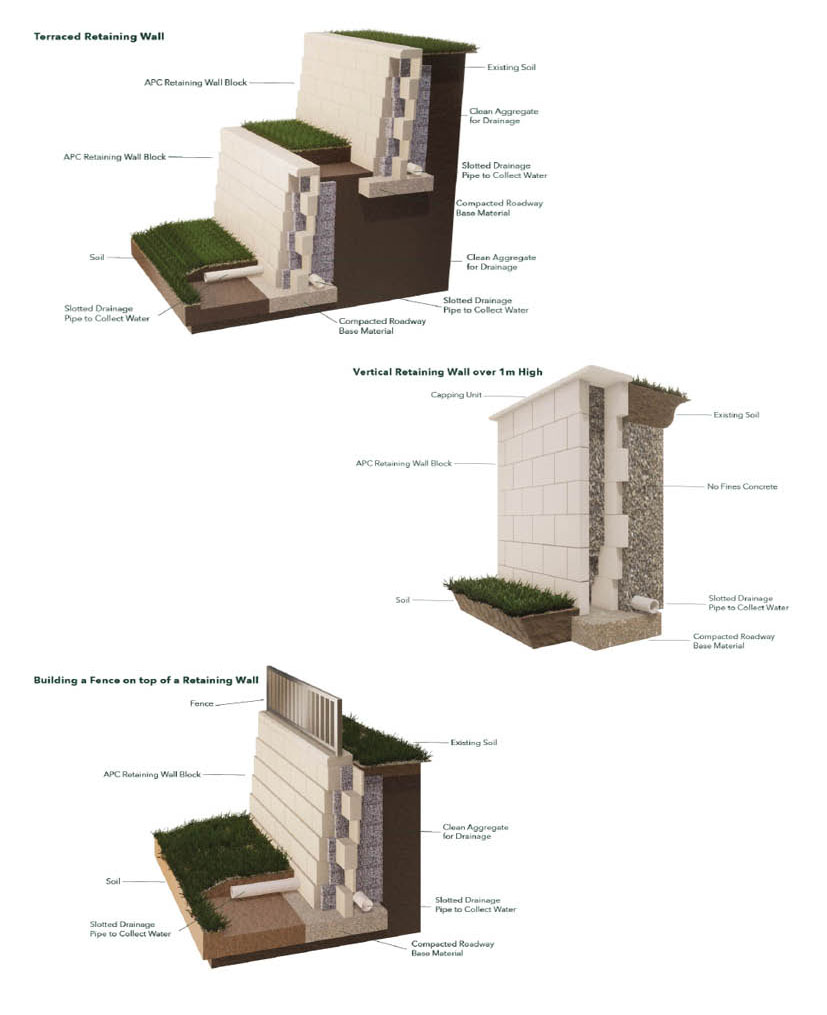
What is no Fines Concrete (NFC)?
Basically, it is just what the name suggests, concrete without any fine aggregates or sand. It consists of generally an aggregate (gravel), cement and water.
The aggregate is coated with the cement slurry binding it together. It dries with the strength of concrete but with voids or air pockets. This makes the NFC light weight and allows water to pass through its honeycomb texture.
NFC can either be mixed on site for smaller areas or purchased from a reputable concrete supplier and trucked in for larger commercial applications. NFC cannot be pumped using a concrete pump
NFC is mixed at a 6:1 ratio by volume of 20mm maximum size clean aggregate and cement. Water content should be such that the cement slurry evenly coats the aggregate and retains a wet/glossy appearance without excess slurry running off. This is typically around 40 liters per 100kg of cement.
With the use of NFC we are able to build Block Retaining Walls in areas and situations where normal construction methods would not work. Some of these situations are:
In areas where excavation behind the wall is limited either due to being on a boundary or close to other structures or footings.
To construct a wall to a greater height than standard gravity wall construction methods.
By using NFC you are basically increasing the depth of your retaining wall. Most masonry blocks would be an average depth of 200-250mm. By using NFC you are increasing that depth of your solid masonry block from 200mm up to 500mm (infill depth) or more depending on the height of your wall.
It is always recommended that every 3rd or 4th block should have part of the back edge removed. This would give a far better adhesion tying the NFC infill layer and the NFC core filled blocks creating a far stronger structure.
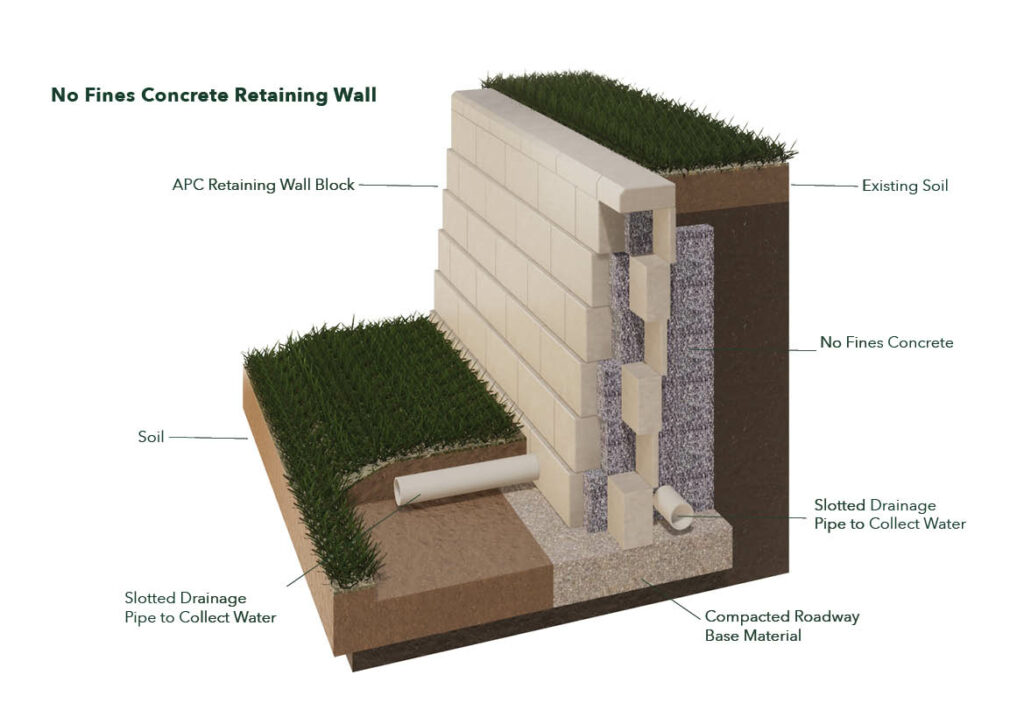
Contrary to popular belief, building a fence on top of a behind a block retaining wall is rather easy!
In some cases where only a small amount of retaining is required as in 200-400mm, the fence can be built directly on top of the wall with the fence posts passing through the walling blocks and concreted into the ground as normal. This method would be ok to use with all forms of fencing such as post and rail, colour bond post and rail, good neighbour fencing, tubular panel and even pool fencing.
If the block retaining wall is more substantial as in a meter high or more than, a fence would have to be behind the wall instead of through or on top. Some segmental retaining wall blocks do not have a big enough cavity or void for the fence post to be directly concreted inside them and would lack the strength to hold the weight of a fence. Check with your local APC store on the most suitable block.
Generally, most walls are built using an aggregate (gravel) backfill or in some circumstances No Fines Concrete (NFC). Because of this an allowance has to be made for the fence post at the early construction stage such as installing PVC piping as a sleave for the fence post to fit into – this would require some forethought and good planning.
Block retaining walls are light weight, cost effective and easy to build. They come in a wider range of styles and colours and are more versatile than concrete sleepers, creating curves and tiered walls can be achieved with ease.
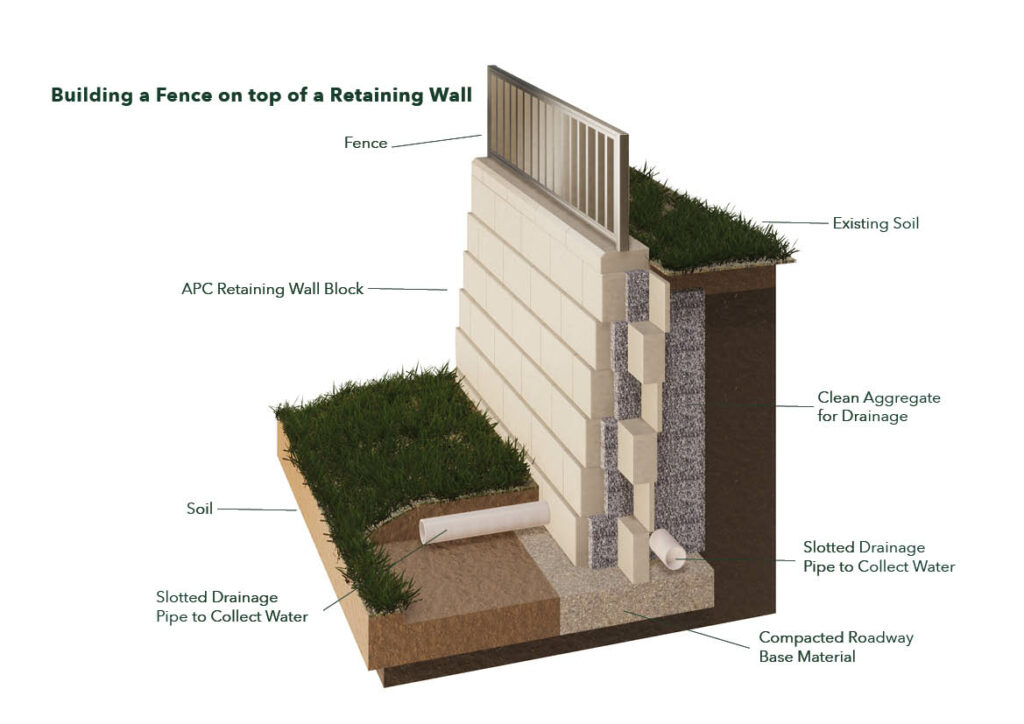
STEP BY STEP GUIDE
STEP 1 : CHECK COMPLIANCE
Check with your Local Council to ensure all local Building Codes are complied with.
Step 2 : Preparing the subgrade
The subgrade should be compacted by several passes of a mechanical plate vibrator. Where there are significant variations of subgrade or compaction soft spots, or where there is ponding of ground water, the material shall be removed, replaced and compacted in layers as per engineer’s advice. Trenches shall be dewatered and cleaned prior to construction, such that no softened or loosened material remains.
Step 3 : Base
The facing shall be built on a base not less than 150mm thick, consisting of one of the following options:
* Compacted crushed rock, well graded and of low plasticity (without clay content), compacted by a plate vibrator;
* Cement-stabilised crushed rock, with an additional 5% by mass of FP Portland cement thoroughly mixed, moistened and compacted by a plate vibrator; or
* Lean-mix concrete with a compressive strength of not less than 15 MPa.
Step 4 : First course
Spread 25mm of washed sand over the compacted base.
The first course is now bedded into the washed sand. The use of a level and string line is recommended to ensure the first course is laid correctly. Ensure each block is also well filled with clean aggregate.
Step 5 : drainage and backfill
Place 100mm diameter PVC agricultural pipe with sock behind the wall, with a 1 in 100 fall. Backfill behind the courses of blocks to a width of approx. 200mm – 300mm using 10-20mm clean aggregate. Ensure each block is also well filled with clean aggregate.
Step 6 : laying additional courses
Lay the next course and subsequent courses to a string line following the same procedure, as outlined in Step 4, cleaning the top of the blocks, filling the block cores and backfilling behind the blocks to a maximum of one block high, at a time (as per Step 5).
Step 7 : Capping units
Glue to capping unit with tiling cement.
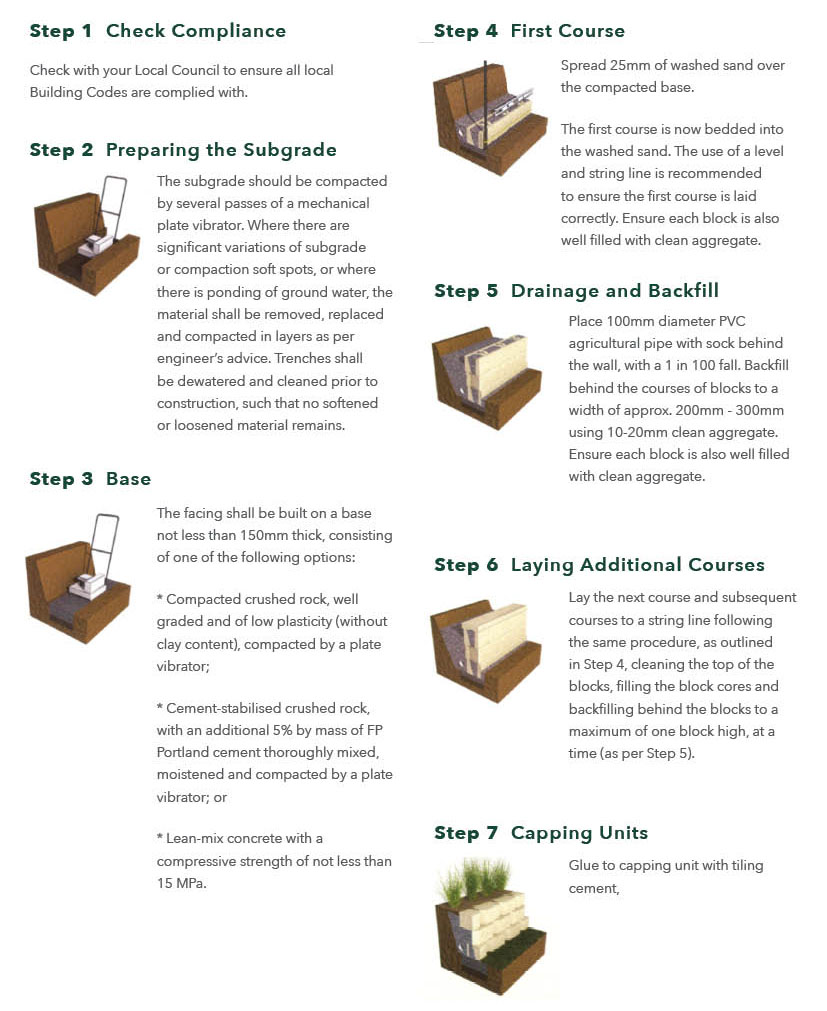
STeps
Steps must be built in accordance with local building codes.
Typically use a 300mm wide bullnose capping block for the step tread.
Typically a 150-175mm step rise is preferred, max step height is 190mm.
IDEAS AND INSPIRATION
Retaining walls can be necessary when you need to retain large amounts of soil. When you have a sloping block, it’s important to properly retain and hold the soil to create your living spaces. Tiered blocks using retaining walls is a great way to maximise your block.
Your retaining wall can look great with the vast amount of retaining wall block products on offer. However, you can go a step further and use your retaining wall to create some highly functional and striking features in your yard.
We provide you with some inspiring ideas and tips, to get you working towards your creative retaining walls that provide a dual purpose.
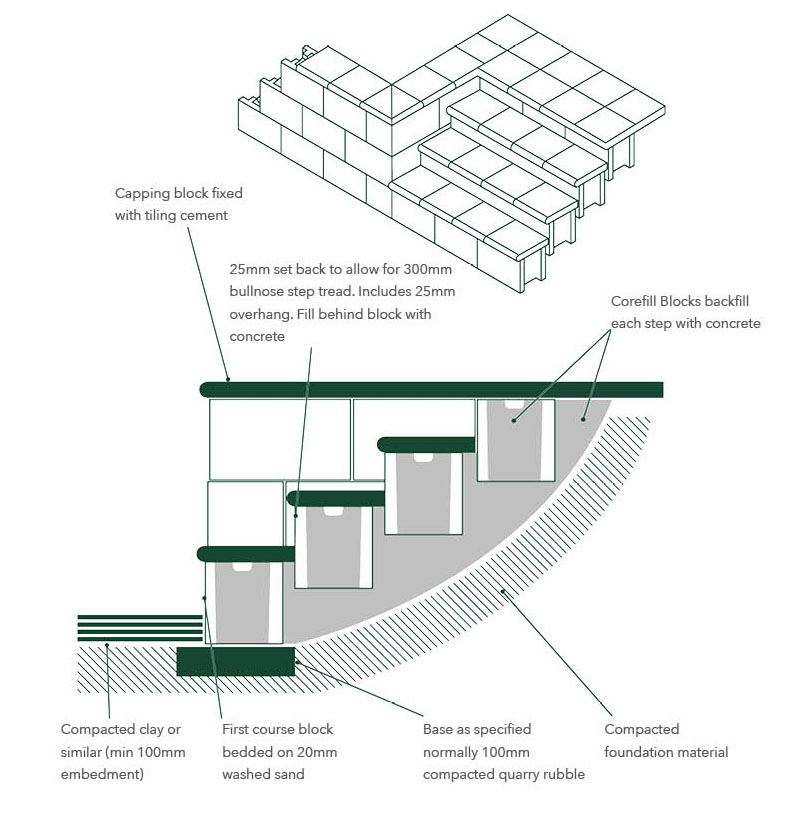
seating spaces
Use your retaining wall for seating and entertain your guests at the same time! Creating in-built permanent seating makes your retaining wall not only essential but practical too.
Fire pits
Fire pits are not just a great way to keep warm during the cooler months but are also a great space to gather when entertaining friends and family.
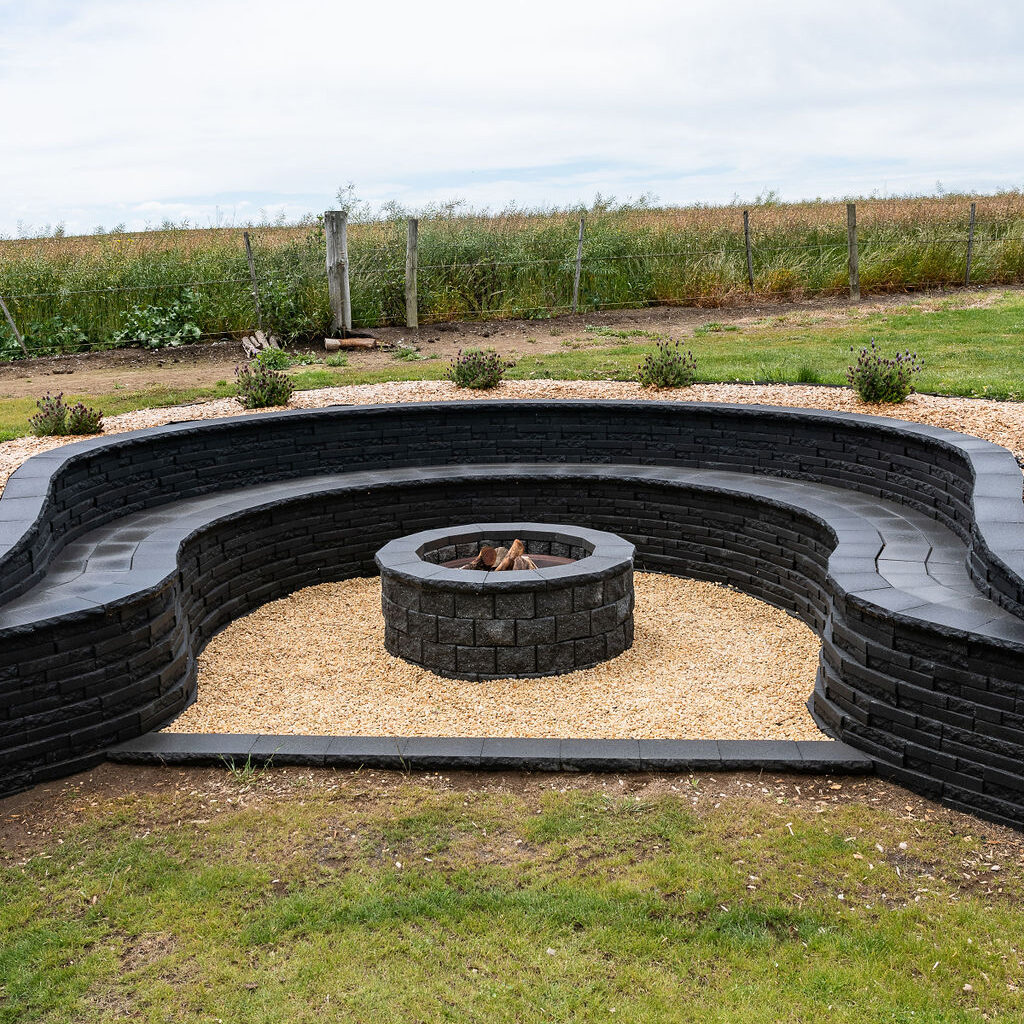
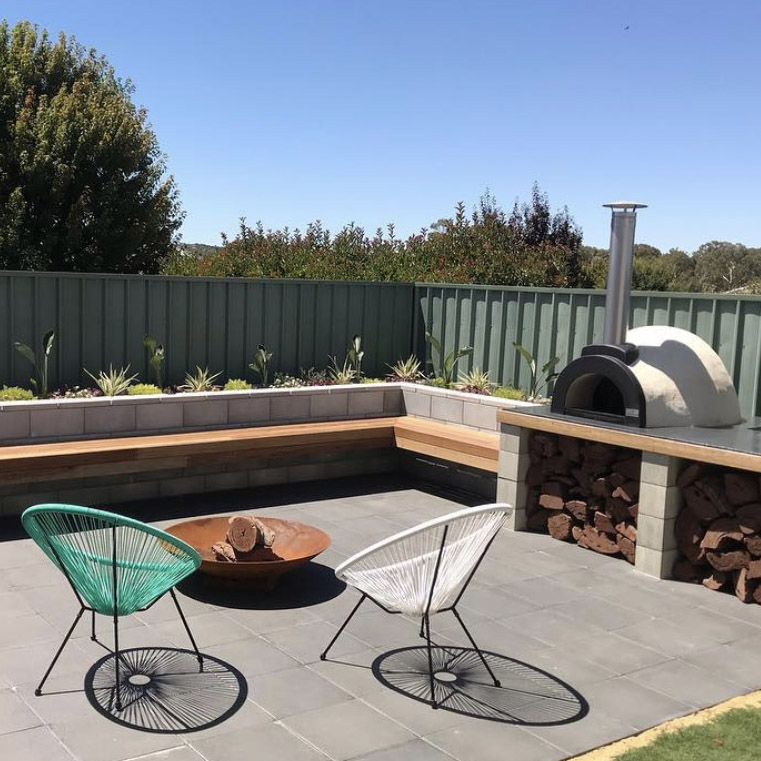
Creative garden beds
Create various garden beds within your retaining walls. Build these at various levels or curves to create some eye-catching features.
Sunken Courtyards
Creating a sunken courtyard in your backyard makes an impressive feature and a great space to relax and entertain. Take it a step further and incorporate a fire pit so you can make the most of your space all year round.
vegetable gardens
Double your retaining wall as a place to grow a veggie garden! This will maximise the space of your backyard by using it to also grow your own produce.
Add Some Steps or lighting
Add some visual impact with incorporating lighting with your retaining wall. If you are incorporating steps into your retaining wall, lighting will not only create a striking feature but also provides safety.
Create different shapes and mix colours
Don’t be afraid to mix up your retaining wall block colours – different sections could use different colours or use a different coloured capping unit.
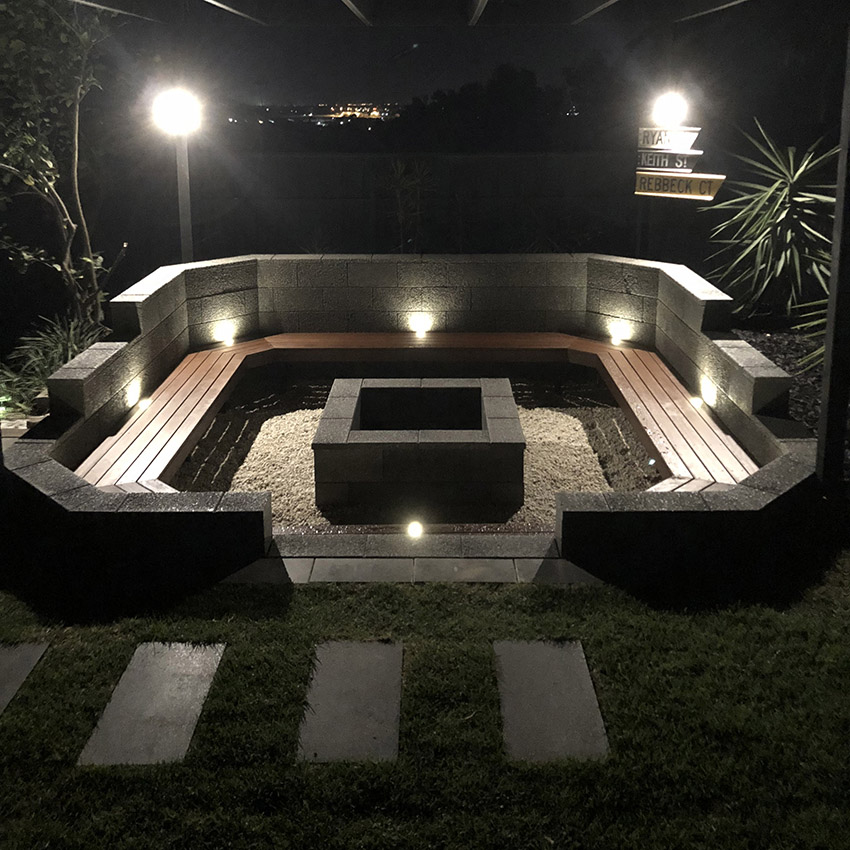

Top 10 tips for easy Delivery
Delivery of your pavers, bricks or retaining wall system is the first exciting step in the construction of your project. We at APC take pride in efficient and effective delivery of our products to your site. A few simple guidelines will help us help you in placing your product where you want it, when you want it.
1. Estimate accurately. We can help you estimate you requirements to avoid over or under ordering.
2. Not so fast! Have your product delivered to site at least one day before starting work. Starting work on the delivery day may lead to lost time due to waiting.
3. Take as much product as you can on each delivery. Ordering a full load ensures priority delivery and allows tradesmen to blend from multiple pallets ensuring an even mix of colours in blended products.
4. Trucks are big! We need to know if there are any obstacles for the trucks such as clearways, main roads, one way streets, schools, hospitals, weight restrictions, a land mark if on a main road etc.
5. Is your site prominent? Place a “site sign” on your front fence or boundary to eliminate any confusion.
6. Is the site locked? We need to know access times. If you require us to enter through a neighbor’s property, it is your responsibility to gain prior written permission.
7. Where do you want them? Consult with your Tradie on best place for delivery and inform our sales staff where your delivery is to be placed. You want your delivery to be in a convenient location, without being in the way. Place markers where possible. Our tractors need at least 2.5 meters clear width and 2.1 meters height clearance.
8. A forklift with a pallet weighs about 5 tonnes. It is your responsibility to ensure the ground and any path or driveway that has to be crossed can take the weight. Storm water pipes are particularly vulnerable to damage.
9. Safety first! Ensure children and pets are well out of the way during delivery. Our delivery drivers will do their best to place pallets in the locations required but they have the final say when it comes to safety and possible site damage and damage to their vehicles.
10. Delivery times. A minimum of 48 hours is usually required to organise your deliveries. We cannot guarantee exact delivery times, as heavy vehicles can be affected by traffic and difficult sites.
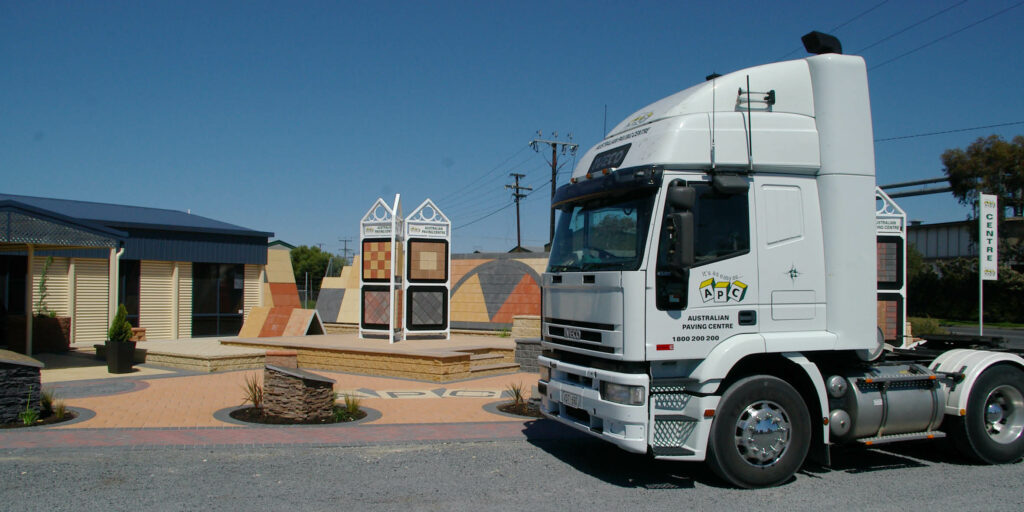
Tips on how to find the right tradie
When it comes to paving or retaining walls, you’ll need to consider whether you’ll hire a professional contractor or DIY. You can hire a licensed contractor and they can do the job for you, guaranteeing quality of work.
At Australian Paving Centre, we can put you in touch with local paving and landscaping contractors. You can request a quote online and we’ll put you in touch with the right Tradie for your project. Our preferred tradies operate independently of APC. We do our best to match a local tradie to your project, however you must conduct your own due diligence on these businesses. Please ensure they are currently licensed and insured for the work they are undertaking.
Find someone local. Local tradies should respond to quotes quickly because they are concentrating on work in their local area. If they are local, they are generally on-site more often and readily available to attend to the project for any rectification work or additional small jobs. If you don’t use a local tradie in the first instance, it is most difficult to get the same tradie back to do a small fiddly job.
Your local tradie must be licensed for the work they are quoting to complete. Their builders’ license will have a summary of what work they are authorised to do.
Your tradie must be insured in case something goes wrong on the job. Accidents can happen!
The tradie should provide a written quote. It is not unreasonable for them to ask for a deposit prior to starting the job. A deposit of between 33% and 50% is fair for the small operators.
Ask to see some local work similar to what you are asking them to quote and inspect it.
Look for the local tradies’ Facebook page or Instagram page and check out their work. Some have websites, but most are very basic. If they don’t have a website, this should not deter your choice because a lot of these tradies do not have a website. Good tradies find their work through word-of-mouth and referrals. The tradies having to rely on service-based internet companies for quotes may not produce good quality work.
Try not to use a business where the person quoting the project does not work in the industry in a hands-on capacity. Many people find that those that only quote the jobs and do not get involved in installation invariably over promise and under deliver. These types of business structures are more expensive due to higher operating costs of covering the salesperson or the quoter as well as the installation team.
For best results and better value for money, use the small business owner-operators who quote and build the project they have quoted for you. When the Tradie who quotes the job builds the job, you get a much better result of what you are looking to achieve.
Research and purchase the pavers, retaining wall and landscaping products yourself. It provides a cheaper overall cost for your paving, landscaping or retaining wall project and you buy the product you like and not the product the Tradie makes the most money out of.
Key tips to prepare for your project
1. Some walls over 800mm in height MUST be designed by a qualified and experienced civil or structural engineer with a comprehensive working knowledge of soil mechanics and structural analysis and design. It may be a Council requirement to have the wall certified and supervised by a civil or structural engineer.
2. DIAL BEFORE YOU DIG Before undertaking any project that requires excavation, it’s imperative you call Dial Before You Dig on 1100 or visit www.1100.com.au. Digging into the ground runs risk of hitting electrical lines, data cables or storm water pipes so take advantage of this free service that can supply you with details of where the services run on your property.
3. POISON THE GRASS This tip will save your back big time, don’t worry, you can thank us later. We recommend poisoning the grass in the area you will be excavating two weeks before you excavate.
4. PREPARING FOR YOUR DELIVERY If you’ve ordered your APC products for delivery, please consider access to the property. If you can, please prepare a safe and wide areas for the forklift to drive through. Forklifts require a clearance of 2.8 metres wide and may have height restrictions.
5. SAFETY TIPS Always wear eye and ear protection when cutting blocks or using a compactor. Bend your knees when lifting heavy blocks. Wear work boots to protect your feet and gloves to protect your hands. Slip, slop, slap if you are working in the sun. Building your own retaining wall takes time so also ensure you drink plenty of water to keep hydrated.
6. Start at the lowest point or start from the corners and work out from there. Make sure all walls are locked in and pushed forward. Then compact fill before applying capping units.
7. There is no such thing as too much drainage!
8. Never cut corner units, only blocks when needed,
9. Use short screed bars in your trench. This will make it easier and quicker to prepare the base course.
10. Ensure you order everything you need at once and set aside an allowance for breakages and cutting.
11. Wherever possible keep walls under 1 metre high – better to terrace a 2 metre embankment with 2 x 1 metre walls than build 1 x 2 metre high wall.
12. Seal your retaining wall with a sealer. This can simply be applied with a roller or sprayed on depending on what type of sealer you are using and what type of walling blocks. If sealing your wall, we recommend you do this as soon as possible after you’ve installed your wall before it gets too dirty.
13. In some instances, efflorescence may appear with some concrete products which is a natural occurrence and looks like a white ‘chalky’ marking on the surface. These markings can disappear on their own over time but if you’re wanting to get rid of it quickly, you can get some ‘Anti Eff’ which contains strong acids to remove it but be sure to read and follow the instructions carefully.
14. If you decide not to ‘Do it Yourself’, APC recommends to always use a licensed builder and to sight their current license to ensure they are licensed to carry out the work quoted and subsequently installed. All work must be carried out to Australian standards.
View our extensive range of retaining wall blocks here
Need help choosing your blocks?
Wall Builder
Use our Wall Builder to help choose the right retaining wall block for your project
Request a Quote today!
Send us a product enquiry or request a quote online
We have the best retaining walls range in Adelaide to choose from. Visit your local APC store near you to view our amazing retaining wall displays. For those who are handy, we have a huge range of DIY Retaining wall information to help you through every step of building your retaining wall. Alternatively, we have preferred local Tradies to quote for any retaining wall installation.
At APC, our DIY Retaining Wall guide provides you with step by step instructions, information and tips and tricks for building your retaining wall. We have a range of DIY retaining wall blocks to make the job easier.
The cheapest retaining wall block is our economical Textured Easy Lock block. Retaining wall blocks are generally cheaper than concrete sleepers. Retaining wall blocks are easier to handle, quicker to install and can be a DIY project. View our economical Textured Easy Lock blocks here.